David Tibbetts, CSP
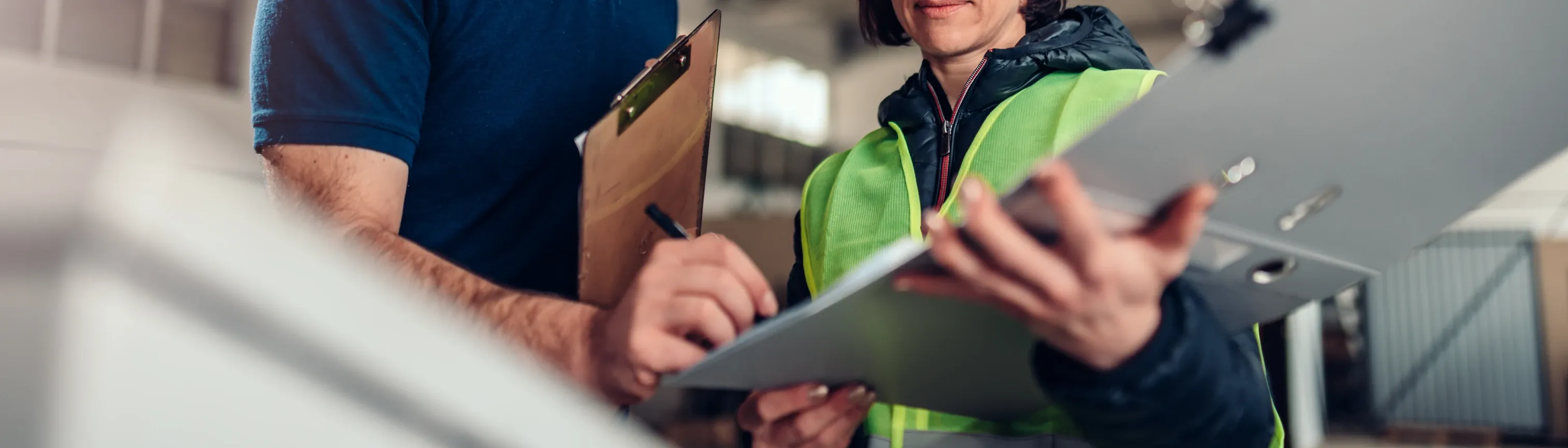
Executive Summary
Asset owners depend on contractors to execute capital projects and maintain existing facilities. Meanwhile, general contractors (GCs) and construction managers (CMs) count on specialty trade partners to complete complex scopes of work on tight timelines to satisfy client demands.
Unfortunately, contractors introduce risk. Understanding and managing this risk becomes more challenging as a business grows and relies on dozens, hundreds, or even thousands of contractors across projects and sites.
A significant safety incident involving contractors can mean the difference between success and failure. Safety incidents impact human lives, can result in project delays, and damage hard-earned reputations. For GCs and CMs, this could mean not winning the next project. For asset owners, this could mean decreased shareholder confidence, negative media coverage, or lost revenue when projects are late.
A disciplined and scalable approach is required to mitigate contractor risks on every project and worksite. When managing wrap-ups such as an Owner-Controlled Insurance Program (OCIP) or a GC’s Contractor-Controlled Insurance Program (CCIP), a sophisticated contractor management program is imperative to realize the program’s financial benefits. In existing facilities, such as data centers, advanced manufacturing plants, and health systems, negative impacts on uptime, production, and patient well-being are unacceptable.
Contractor safety assessment, commonly referred to as prequalification, is a critical component of successful contractor management. But this is just the beginning and must not be viewed as a pass/fail gate. The result should not be just, “Yes, we can use this contractor,” or “No, this contractor is too risky.” In today’s competitive market, eliminating contractors from consideration is not sustainable.
This document provides a comprehensive guide to contractor safety management based on a modern approach to contractor management – one that seeks to make all of your contractors successful. By implementing the strategies and tools outlined in this guide, asset owners and GCs can better understand the risks presented by contractors, develop plans to address identified risks, and, importantly, monitor each contractor's performance throughout their relationship.
The processes outlined here facilitate collaboration and communication between all parties to deliver successful outcomes, strengthen relationships, and support continuous improvement.
We call this “Contractor Success” and believe strongly that it is delivered through continuous risk mitigation.
The Shortcomings of Traditional Prequalification
Traditional methods for managing contractors and evaluating their risks have often proven ineffective—limited both by flawed frameworks and the mindset behind their execution. The following sections outline these key challenges.
Prioritizing the Wrong Safety Data?
The most common challenge that organizations face is that their manual processes are not scalable and, therefore: 1) do not deliver consistent and meaningful results; and, 2) tend to focus only on one or two lagging safety metrics such as EMR or TRIR because this information can be gathered relatively easily.
Manual processes consume valuable time, preventing safety professionals from focusing on higher-value tasks like reviewing risks and creating action plans. The time spent collecting and analyzing contractor documents is inefficient.
Valuable insights in contractor safety programs often go unnoticed because manual document reviews are impractical. Safety manuals are collected from contractors and sit on shelves or in files only to be reviewed when an incident occurs or a regulatory agency arrives on site.
Some organizations use software that provides a pass/fail outcome, which can be overly burdensome for contractors to complete, creating friction and potentially damaging relationships.
The Problems with Pass/Fail Prequalification
A mistake many organizations make is viewing the prequalification process as a pass-or-fail exercise. Thresholds are set, and if exceeded, a contractor is eliminated from consideration. Their safety standard may read:
- Contractors with an Experience Modification Rating (EMR) exceeding 1.0 will not be considered.
- Contractors with a Total Recordable Incident Rate (TRIR) above 2.0 will not be considered.
- Contractors with one or more fatalities in the last three years will not be considered.
Although each factor is typically part of the process, eliminating contractors based on any single criterion creates friction and may exclude qualified contractors from the bidding process.
Finally, it is important to recognize that assessing contractor risks during prequalification is just the beginning. Many organizations do not continue to actively monitor performance and identify emerging risks when the contractor arrives on site and begins work. This is especially important for the subset of contractors that present the most risk as identified through prequalification.
Continuous Risk Mitigation
Contractor Success is delivered when organizations implement a continuous approach to risk mitigation. We believe this can be simplified into three phases, each of which answers an important question:
- Prequalify - What risks does this contractor present?
- Plan - What are we going to do about identified risks?
- Execute - How is this contractor performing?
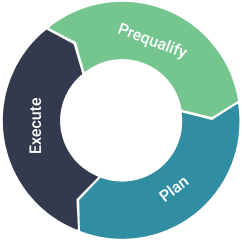
Prequalify: What Risks Does This Contractor Present?
To answer this question, safety assessments need to deliver insights into both a contractor’s past performance and the sophistication of their organization’s safety policies and procedures. Looking only at one or the other can create blind spots.
Imagine a contractor with poor past performance as indicated by an elevated EMR, a fatality in the last three years, or an elevated days away case rate. An organization might be quick to eliminate this contractor from consideration. What if this contractor has learned from past incidents, introduced new programs and training, committed to a strong safety culture, and can clearly articulate a vision for ongoing improvement?
Now imagine a contractor with robust safety programs and sophisticated management systems that can provide training documentation and evidence of a pre-task planning or job hazard analysis process. All of these things look good on paper. But without looking at their performance history, you may miss meaningful insights. If this contractor has poor past performance, it may indicate that the programs and documentation provided are not translating into the safe execution of their work.
Indicators of Past Performance or Lagging Indicators
Past performance is crucial. Analyzing it provides valuable insights for meaningful discussions with contractors. These metrics should be used together to guide conversations that uncover the reasons behind performance and the improvements being implemented.
Understanding contractor performance varies between the U.S. and other countries. This section highlights those differences and offers approaches for both U.S. and international contractors.
Assessing Past Safety Performance in the United States
Incident Rates and Benchmarks
The metrics below provide key indicators of a contractor's past safety performance, focusing on incident frequency and severity
Metric | Purpose | Thresholds |
---|---|---|
TRIR | Total Recordable Incident Rate - a measure of the frequency of ALL injuries or illnesses that required medical treatment beyond basic first aid. This includes DART cases, lost time cases, and cases involving restricted duty or job transfer. | >25% above industry benchmark |
DART | Days Away, Restricted Duty, or Job Transfer Rate - a measure of the frequency of incidents resulting in days away from work, restricted duty, or job transfer for the affected employee. DART cases are a subset of recordable cases with a more severe outcome. | >25% above industry benchmark |
LTIR | Lost Time Incident Rate - a measure of the frequency of incidents resulting in the affected employee missing one or more days of work. | >25% above industry benchmark |
The Bureau of Labor Statistics releases annual incident rate benchmarks for each trade. By comparing a contractor's average incident rates over the past three years to the latest industry benchmark for their specific trade, valuable insights can be gained. If a contractor’s average incident rates are much higher than the industry benchmark and are increasing year over year, a deeper review is warranted to understand the following:
- The total number of recordable incidents
- The number of recordable incidents resulting in days away from work, restricted duty, or job transfer
- The average number of days away from work per lost time case.
- This provides a measure of the severity of incidents that are occurring. If there are more than 7 days away per lost time case the severity of incidents is relatively high.
- The percentage of DART cases that involve restricted duty or job transfer.
- This indicates whether or not the contractor has effectively implemented a return-to-work or modified duty program. An effective return-to-work program can significantly reduce the costs associated with incidents. Managing claims costs is always important but is especially important on projects enrolled in an OCIP or CCIP.
Experience Modification Rating (EMR)
Safety Metric | Purpose | Thresholds |
---|---|---|
EMR | Experience Modification Rate measures a company's injury and claims experience against like-sized companies performing similar scopes of work. An EMR of 1.0 is average; values below 1.0 indicate better-than-average experience, while values above 1.0 suggest higher risk. Calculated by insurance carriers based on the frequency and severity of claims and payroll size over three years. | >1.15
>1.00
<=/1.00
|
Although the industry recognizes that EMR has limitations and was not originally designed as a comprehensive measure of contractor safety performance, it remains a widely used metric that offers some value. However, EMR should be applied as one of several evaluation criteria—not as a standalone determinant—and it should never be used to automatically disqualify contractors. Notably, states such as Virginia (2016) and Texas (2023) have passed legislation prohibiting the exclusion of contractors solely based on EMR thresholds.
EMR provides a snapshot of a contractor’s safety performance by comparing their claims experience against similar-sized companies engaged in comparable work. An elevated EMR can have significant business consequences, including higher insurance costs. It is essential to ask thoughtful, probing questions to understand the drivers behind an elevated EMR.
- Were there a significant number of claims?
- Were there one or two significant incidents with high claims costs?
- What were the circumstances and learnings from the incidents that resulted in the elevated EMR?
Previous OSHA Violations
The use case for understanding OSHA citation history is clear, but there are simple questions that provide additional insight.
- Has the contractor been issued any OSHA citations in the previous three years?
- If so, what was the severity (Other than Serious, Serious, Repeat, or Willful)?
- What standards were specifically cited?
After clearly understanding a contractor’s previous OSHA citations, it is important to learn what the contractor has done in response. The discussion should focus on organizational improvement instead of seeking to understand how a citation was abated in the eyes of OSHA. An OSHA citation was issued as a result of a standard being violated. The implication is that one or more employees were put in harm's way as a result.
What is the contractor doing to prevent a similar exposure from occurring again?
Assessing Past Safety Performance Internationally
Incident Rates and Benchmarks
Assessing international contractors requires a similar but adjusted approach, with attention to country-specific reporting and recordkeeping rules. Key considerations include when injuries must be reported, how a days away case is defined, and whether industry benchmarks for incident rates are published. Here are some examples:
- Ireland requires employers to report any injury that results in an employee being unfit for duty for more than three days.
- The United Kingdom requires employers to report any injury that results in over-7-day incapacitation of a worker. Employers must record any injury that results in over-3-day incapacitation.
- The Netherlands requires employers to report any injury that results in over 3 days of sick leave.
As you can see, this is quite a different definition of a lost time or days away case in the US, which requires recording and reporting of any injury that results in one or more days away from work.
Ireland and the United Kingdom both publish industry benchmarks on an annual basis. The Netherlands does not, but there are sources, such as Eurostat, where benchmarks for the Netherlands and other European countries can be found. Unlike the United States, which publishes benchmarks for each trade within an industry (electricians, plumbers, painters, steel erectors, etc.), many international countries publish benchmarks at the industry level only (construction, manufacturing, mining, etc.).
One more nuance is the country’s approach to calculating and measuring incident rates.
Country | Incident Rate Measurement |
---|---|
🇺🇸 United States | Number of incidents per 100 workers per year |
🇩🇪 Germany | Number of incidents per 500 workers per year |
🇮🇪 Ireland | Number of incidents per 1,000 workers per year |
🇬🇧 United Kingdom | Number of incidents per 100,000 workers per year |
🇪🇺 Eurostat | Number of incidents per 100,000 workers per year |
The result is industry benchmarks for lost time incident rates that look much different from country to country. Here are examples using incident rates published for construction:
Country | Lost Time Incident Rate Benchmark for Construction |
---|---|
🇺🇸 United States | 1.0 lost time incidents per 100 workers per year |
🇩🇪 Germany | 29.7 lost time incidents per 500 workers per year |
🇮🇪 Ireland | 14.3 lost time incidents per 1,000 workers per year |
🇬🇧 United Kingdom | 740 lost time incidents per 100,000 workers per year |
🇪🇺 Netherlands (Eurostat) | 1,264 lost-time incidents per 100,000 workers per year |
When available, a contractor’s past performance should be compared against country-specific benchmarks.
In countries without clear injury reporting requirements, it may be necessary to take a different approach to evaluate contractor safety performance. One option is to create a simplified version of US reporting standards using general, descriptive language—avoiding terms like “recordable case” or “DART case.” Contractors can then be asked to provide this information for each of the past three years.
Occupational Injury Details | 2024 | 2023 | 2022 |
---|---|---|---|
Number of fatalities | 0 | 0 | 0 |
Number of injuries resulting in days away from work | 3 | 1 | 1 |
Number of injuries without days away from work | 5 | 3 | 4 |
Total number of days away from work | 174 | 45 | 82 |
Total number of employees | 101 | 99 | 94 |
Number of hours worked by all employees | 207,338 | 199,746 | 187,392 |
Capturing data this way allows for the calculation of incident rates per 100 workers per year and facilitates comparison to U.S. trade-specific benchmarks.
Regulatory Experience
In the US the Occupational Safety and Health Administration (OSHA) provides a searchable database of violations. This allows asset owners and GC’s to identify whether or not a contractor has been cited in the past.
Outside of the US this is not as common. While the United Kingdom offers a similar database where organizations can search for and identify whether or not a contractor has received any ‘breaches’ or ‘convictions’ due to an inspection conducted by the Health & Safety Executive, most countries do not.
In the absence of a database like the two described above, it is still valuable to ask contractors about their experience with regulatory agencies.
Has the contractor been investigated in the past three years by a regulatory agency?
Has the contractor received any citations, fines, or penalties as a result of investigations?
If the answer is yes to either of the above questions, contractors should be asked to provide more insight into the circumstances that led to the interaction with the regulatory agency and any resulting citations, fines, or penalties. Then the contractor should be asked to describe what they learned from that interaction and steps they have taken or are taking to prevent the exposures that led to the citations.
Past Performance - Summary
The questions raised by past performance risks—and how contractors respond—can reveal a lot. Strong contractors explain how they’re improving, while others may show a lack of understanding or concern. These conversations are themselves indicators of risk.
Leading Indicators, Sophistication, and Culture
Beyond past performance, “leading indicators” offer insight into a contractor’s safety culture, commitment, and overall sophistication.
Programs
First, contractors are required to have programs in place in accordance with regulations. These programs must address the hazards that their employees face in the course of delivering their scope of work. The best programs address the following:
- Which hazards employees may encounter;
- When, or during what activities, hazards are most likely to be encountered;
- What control measures will be implemented to mitigate identified hazards;
- What training ensures employees can recognize hazards and implement controls?
Effective safety programs go beyond simply repeating standards and regulations. While they may reference the applicable standards, they should focus on detailed strategies for addressing the specific hazards associated with the company's scope of work. The following example demonstrates how this may be applied to fall protection:
- When, where, and during what activities are fall exposures most likely?
- How should employees plan their work to identify appropriate fall protection measures?
- What controls are available, in order of priority, to eliminate or mitigate fall exposures?
- How will employees be trained to recognize fall hazards and implement proper controls?
- How will training effectiveness be measured?
If a contractor does not have an adequate program to address a likely hazard, this must be addressed prior to awarding work or at least prior to the contractor starting work on site.
Safety Management Systems
Management systems are important for every part of a business—including safety. Contractors need a structured safety management system to run an effective safety program. These systems help guide and prioritize key safety practices, such as:
- Setting annual goals and objectives
- Conducting inspections and identifying hazards
- Engaging leadership in safety efforts
- Investigating incidents
- Defining a clear safety policy
- Holding people accountable
- Performing annual safety evaluations
- Offering safety incentives or recognition
- Providing employee training
- Involving employees in safety activities
These are just a few examples of how safety management systems support effective execution. Without them, even the most detailed safety programs can fall short. Companies may struggle to measure performance or spot trends, leadership may not recognize the importance of their role in building a strong safety culture, and employees may lack both motivation to prioritize safety and accountability when procedures aren’t followed.
Prequalify - Summary
If a contractor lacks key safety systems and shows poor past performance, it’s a chance to educate them on how structured systems can improve outcomes—a collaborative approach that supports Contractor Success.
Prequalification is just the beginning. A well-rounded evaluation of past performance, safety systems, and culture is essential. No single metric tells the whole story, but together they provide meaningful insights for informed, data-driven conversations. These discussions reinforce that safety is a top priority for the asset owner, GC, or CM.
Plan: What Are We Going to Do About Identified Risks?
The planning elements outlined in this section are informed by the previous phase - Prequalify. It is worth noting that time spent during the Plan phase is focused on the subset of contractors that present the most risk. Some contractors will present low risk based on exceptional past safety performance and highly sophisticated systems. These contractors will be onboarded in accordance with established processes. Extra time spent with at-risk contractors is time well spent. A likely outcome is a project- or site-specific corrective action plan (CAP) that defines how the contractor will be managed to success.
Consider the scenario below:
A contractor had a fatality 18 months ago, resulting from a fall. The contractor received two serious OSHA violations as a result. One for improper use of fall protection equipment and one for inadequate training related to fall exposures. The contractor’s scope of work on your project or at your site will involve a significant amount of work at height. The contractor explained the circumstances that led to the fall and explained how the OSHA violations were abated. The contractors' work on your project or site will involve supported scaffolds, aerial lifts, and ladders and pose fall hazards.
After discussions, the contractor is awarded the scope. However, to ensure attention to fall hazards and proper equipment use, the contractor must create a CAP outlining steps to eliminate or reduce fall risks, train employees on equipment use and inspection, and monitor on-site performance.
Risk Factor | Action |
---|---|
Fall-related fatality and subsequent OSHA violations | 18 months ago, we experienced a fatal fall incident. OSHA cited two serious violations: improper use of fall protection and inadequate training. We have since updated our fall protection policy and retrained all employees. Our scope of work on this project would involve extensive work at heights, including the use of scaffolds, aerial lifts, and ladders. To mitigate these risks, we will: 1. Train all workers on site-specific fall protection requirements, including proper use of harnesses, tie-off methods, and safe use of ladders, lifts, and scaffolds. 2. Perform daily fall hazard assessments and equipment inspections by a competent person. 3. Assign a foreman as the on-site safety lead to monitor work being conducted at heights and enforce safe practices. 4. Ensure only trained personnel use lifts and ladders, and that scaffolds are properly built and inspected. 5. Hold weekly safety check-ins to review field observations and reinforce expectations. |
No full-time safety manager | Today, Babilonia Roofing does not employ a full-time dedicated safety manager. Per our contract agreement we have hired a safety consultant that will visit the project twice per week to conduct inspections, help prepare and modify job hazard analysis, and conduct training focused on current jobsite activities and any areas of emerging risk. |
When developing a CAP, it’s crucial to outline how performance will be monitored. Many organizations struggle or fail at this step.
- How will performance be monitored, and who will be responsible?
- How frequently will teams meet to review performance?
- Which specific key performance indicators will be reviewed?
- How will emerging risks be addressed through revisions to the CAP or other measures?
Frequency | Meeting Type | Purpose |
---|---|---|
Weekly | Schedule, Data, and JHA Review | On a weekly basis our Project Manager, Foreman, and Safety Consultant will meet with the project team to: 1. Review the next week’s schedule and identify any high-risk or non-routine work. Existing JHA’s will be revised or new JHA’s will be developed accordingly. 2. Review aggregated inspection data, discuss, and address any emerging trends. Retrain workers and/or adjust JHA’s. 3. Review current JHA’s to make sure they are relevant and adequately address hazards that are present on site. Ensure that all crew members have reviewed and been trained to understand elements of the JHA’s. |
Monthly | Management System Audit | On a monthly basis we will collaborate with the GC to conduct a management system audit. Making sure that deliverables are being executed including: 1. Orientation 2. Substance Abuse Testing 3. JHA Review 4. Frequency of inspections 5. Toolbox talks 6. Incident investigations 7. Participation in weekly foreman’s meetings |
Execute: How is this contractor performing?
Prequalification has provided insights into contractor risks and informed decisions. CAPs are ready for specific contractors, and now it's time to execute. This section outlines processes and tools to monitor performance and execution.
Inspections
Conducting inspections is an under-valued aspect of managing safety and managing contractors. This may be because organizations use software or a manual process that doesn’t allow them to easily aggregate their inspection data to identify risks. Or it could be that they are frustrated by low-quality inspection data that has failed to deliver any meaningful insights. These are challenges that many organizations face.
The table below provides a simple example of how inspection data can provide critical insights into site safety.
Category | Total Findings | Positive | Negative | % Positive |
---|---|---|---|---|
Personal Protective Equipment | 589 | 412 | 177 | 70% |
Housekeeping | 475 | 304 | 171 | 64% |
Hand and Power Tools | 356 | 270 | 86 | 76% |
Fall Prevention | 104 | 43 | 61 | 42% |
Ladder Safety | 98 | 60 | 38 | 61% |
Total | 1,622 | 1,089 | 533 | 67% |
A strong inspection program is essential and must not be viewed as a compliance exercise. It's an integral component of any safety management system. Aggregated data provides insights that allow organizations to recognize and reward contractors for exceptional performance and also to identify contractors that need improvement in specific areas where risk is increasing.
Inspections play a critical role in assessing and managing contractor safety risks. As highlighted in the CAP example, a key focus should be on fall protection, particularly the proper inspection and use of scaffolds, aerial lifts, and ladders. These targeted inspections and the resulting data will help determine if the CAP is effective. Ideally, inspection data will show that fall risks are being mitigated.
However, if inspection data reveals that unsafe conditions or unsafe behaviors result in fall exposures, it’s time to pause, take a step back, revisit the CAP, and determine next steps to improve performance. There is no time to waste addressing these issues.
Incidents
Every contractor has a company incident history, assessed during prequalification. But how have they performed on your projects? Analyzing incidents on your site—by type, severity, cause, and other factors—provides deeper insights into current performance and can be an indicator of potential future performance.
SIF-potential Events
The construction industry is recognizing the need for new safety metrics and approaches. While total recordable incident rate (TRIR) has dropped by nearly 80% in the last 30 years, fatality rates have remained largely unchanged over the past 15 years.
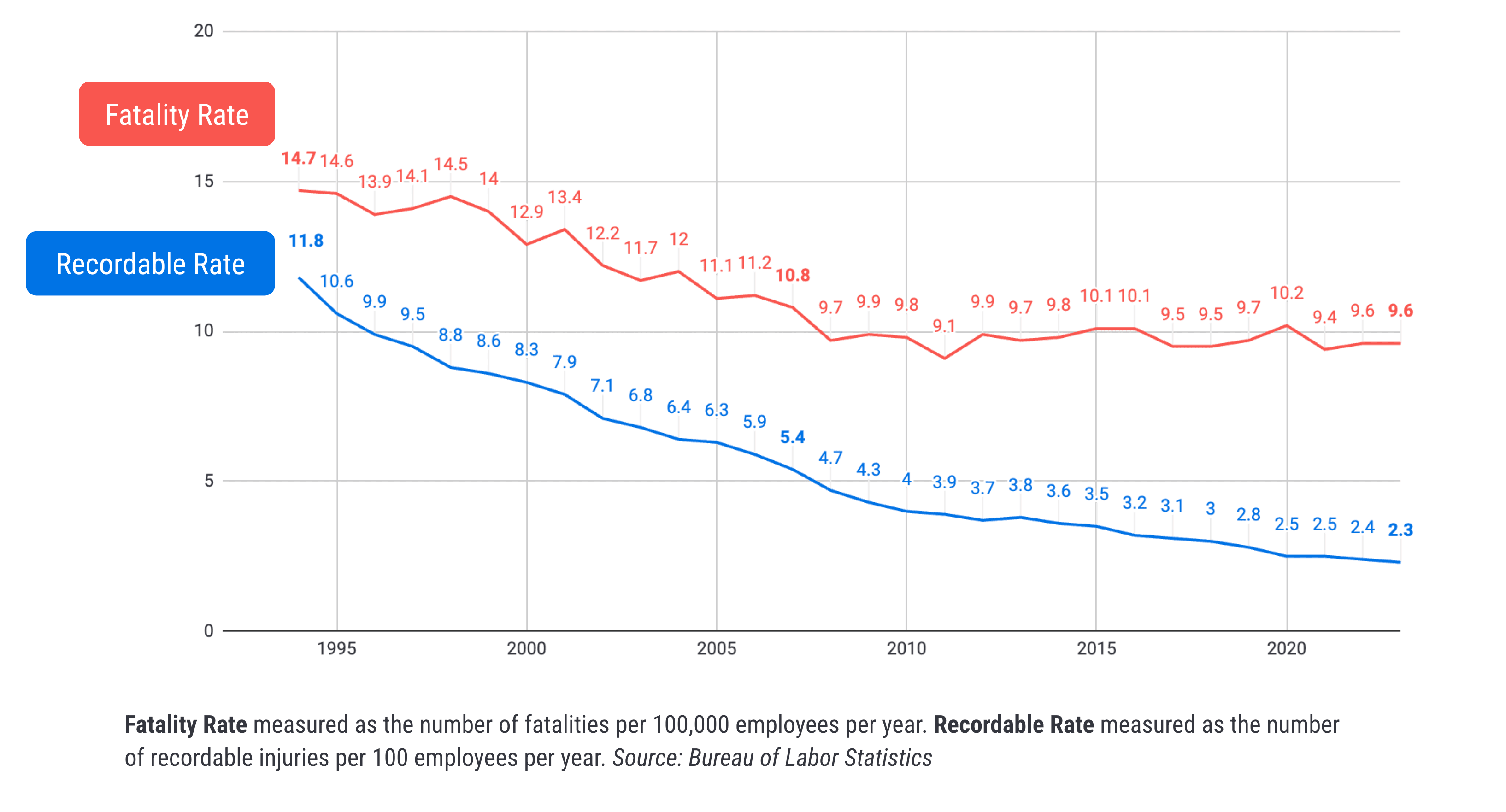
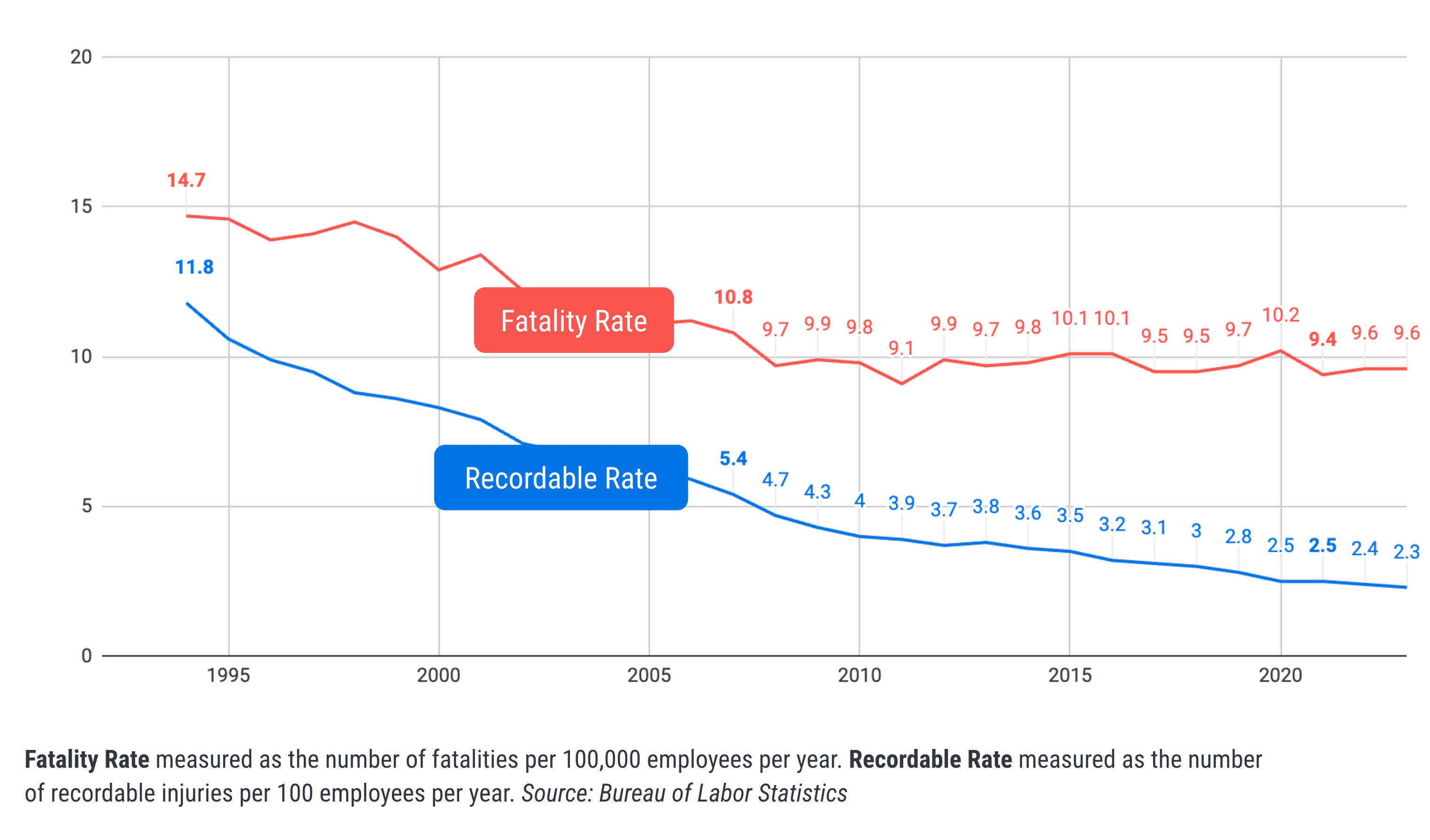
The Construction Safety Research Alliance (CSRA) has conducted extensive research and published valuable resources on this topic SIFs and SIF-potential events.
Organizations should implement processes that focus on high-risk activities, particularly those that could lead to a Serious Injury or Fatality (SIF). A SIF is defined as an injury that is:
- Life-ending - results in a fatality
- Life-threatening - immediate life-saving medical attention was required to prevent a fatality
- Life-altering - the incident resulted in the injured person having permanent or long-term impairment or loss of use of an internal organ, body function, or body part
Although fatalities in construction are too high, they represent a small portion of the overall data and learning opportunities. Therefore, tracking and learning from all events with the potential to resulting in a Serious Injury or Fatality (SIF-p) is a crucial next step.
From a contractor management and contractor assessment perspective, this means being able to answer the following questions:
Has the contractor been involved in any events that had the potential to result in a Serious Injury or Fatality (SIF-p)? Events with the potential to result in a SIF could include a near miss, a first aid case, a recordable or lost-time case, and importantly observation of a high risk behavior or condition.
If the answer is yes, the following questions are important to ask and answer:
What activities have resulted in SIF-p events?
What high-risk/high-energy exposure was present? (Falls from elevation, exposure to energized electrical components, unprotected trenches or excavations, etc.)
What equipment was involved or being used at the time of the SIF-p event?
There is so much opportunity to learn when organizations shift their focus and begin to consistently identify, investigate, and track all events with SIF-potential that have occurred across their projects and sites.
Other Elements of Contractor Safety Management and Assessment
Collecting training certifications for workers, using a pre-task planning process, and implementing a permit-to-work system for high-risk activities (like hot work, work at heights, and critical lifts) are essential elements of contractor safety management that help ensure successful outcomes. These help answer questions like:
- Do employees have the right level of training to recognize hazards and implement controls?
- Are pre-task plans being developed that identify task-specific hazards and controls?
- Are pre-task plans being used to deliver task-specific training on a daily or weekly basis?
- When high-risk work is required, are permits in place, reviewed, and approved before work begins?
Documents collected and produced to answer the questions above are important. But perhaps more important is measuring their effectiveness. Organizations cannot allow these to become ‘paper processes’ or compliance exercises.
Inspection data, in particular, is a key indicator of contractor performance and is an important measure of the effectiveness of training, pre-task planning, and permit-to-work processes. This data helps determine if these process are working and delivering the desired results, answering the following questions:
- Are the contractor’s training programs effective? Are employees retaining the knowledge? Are employees able to translate training into safe work execution?
- Are contractors identifying hazards and effectively implementing controls as work progresses and environments change as a result of an effective pre-task planning process?
- Are contractors following the processes outlined in completed work permits, resulting in safe execution of hot work, well-executed hoisting operations, and implementation of controls to eliminate fall hazards?
Continuous improvement is key to Contractor Success. It involves understanding performance, gathering data to spot successes or risks, and deciding on next steps. Without knowing where contractors and past projects have succeeded or failed, asset owners or GCs struggle to help contractors improve and enhance their own processes.
CCIPs & OCIPS: Unlocking Savings and Profit Through Wrap-Ups
As organizations mature, they often move away from traditional insurance and consider wrap-ups. With traditional insurance, each contractor includes insurance costs in their bid. In contrast, with wrap-ups, asset owners and GCs buy insurance and enroll most contractors under one umbrella policy.
Asset owners can save on insurance by taking on more risk through an owner-controlled insurance program (OCIP). General contractors can also take on more risk, offer savings to their clients compared to traditional insurance, and increase their profit margin with a contractor-controlled insurance program (CCIP). The savings and profit potential grow as the asset owner or GC demonstrates exceptional performance over time.
While insurance savings and increased profits are attractive, organizations must have a strong, scalable approach to selecting the right contractors, assessing their risks, and monitoring performance. Successful execution is key to reducing injuries, claims, and costs. Organizations should only take on the additional risk of an OCIP or CCIP once they have proven, repeatable processes in place.
Continuous risk mitigation, as described in this guide, positions asset owners to realize the benefits of an OCIP and General Contractors to realize the benefits offered by a CCIP. Asset owners can reinvest insurance savings to support organizational goals. General Contractors can win more work, increase profits, and realize continued growth.
The Role of Quality
In construction, there’s a well-known link between quality and safety. When work is done poorly and needs rework, it creates serious safety risks. Crews must remove and replace the original work—often under tighter schedules, added costs, and changing site conditions. This exposes workers to safety risks at least three times: during the original install, the removal, and the rework.
Because of these impacts, it’s important to assess each contractor’s sophistication and approach to quality management. Key questions to consider include:
- Does the contractor have a formal quality control program?
- Do they follow a defined process for quality inspections?
- Are specific inspection hold points established to ensure work is reviewed before moving forward?
- Is there a process for inspecting and accepting materials delivered to the job site, verifying their condition, and properly storing them until installation?
- Does the contractor have a clear process for managing rework and addressing related safety risks?
It’s important to continually evaluate a contractor’s ability to deliver quality work throughout the construction process. Regular quality control inspections should be performed to monitor their performance. The results from these inspections provide valuable data that can help guide future contractor selections, highlighting each contractor’s ability to deliver quality work and fix any issues that arise.
At the end of each contractor’s scope of work, the project team should review the contractor’s overall performance with a focus on quality. This evaluation doesn’t have to be complicated — it can be done by answering a few key questions:
- Was any rework required during the project?
- What was the main cause of the rework?
- Poor quality work
- Incorrect materials installed or materials not installed according to specifications
- Installation of damaged materials
- Did any significant incidents or events with the potential to result in serious injury or fatality (SIF-p) occur during the performance of rework?
By gathering and analyzing data from these evaluations, you can better understand how often a contractor performs rework, the primary causes behind it, and how effectively they manage the added safety risks that come with rework. A formal approach to assessing and monitoring contractor performance relative to quality helps reduce safety risks, keeps projects on schedule and within budget, and supports better, more informed decisions for future work.
Conclusion
Contractor prequalification is more than just a procedural step — it is a critical part of managing risk and ensuring project success. A thorough prequalification process should include sophisticated safety assessments, alongside evaluations of financial health, quality, insurance coverage, and other key risk factors. By following the phases outlined in this guide, asset owners and general contractors can systematically reduce risk, achieve better project outcomes, and build stronger, more collaborative relationships with their contractors.
This guide emphasizes that contractor assessment should be treated as an ongoing process. Through continuous monitoring, regular re-evaluations, and clear communication, asset owners and general contractors can turn safety assessments into a dynamic tool for reducing risk and supporting contractor improvement. These efforts help build a resilient contractor network where safety, quality, and financial stability are top priorities.
By following the approach outlined in this guide, asset owners and GCs can strengthen contractor relationships, improve project outcomes, and foster a culture of continuous improvement and shared success.
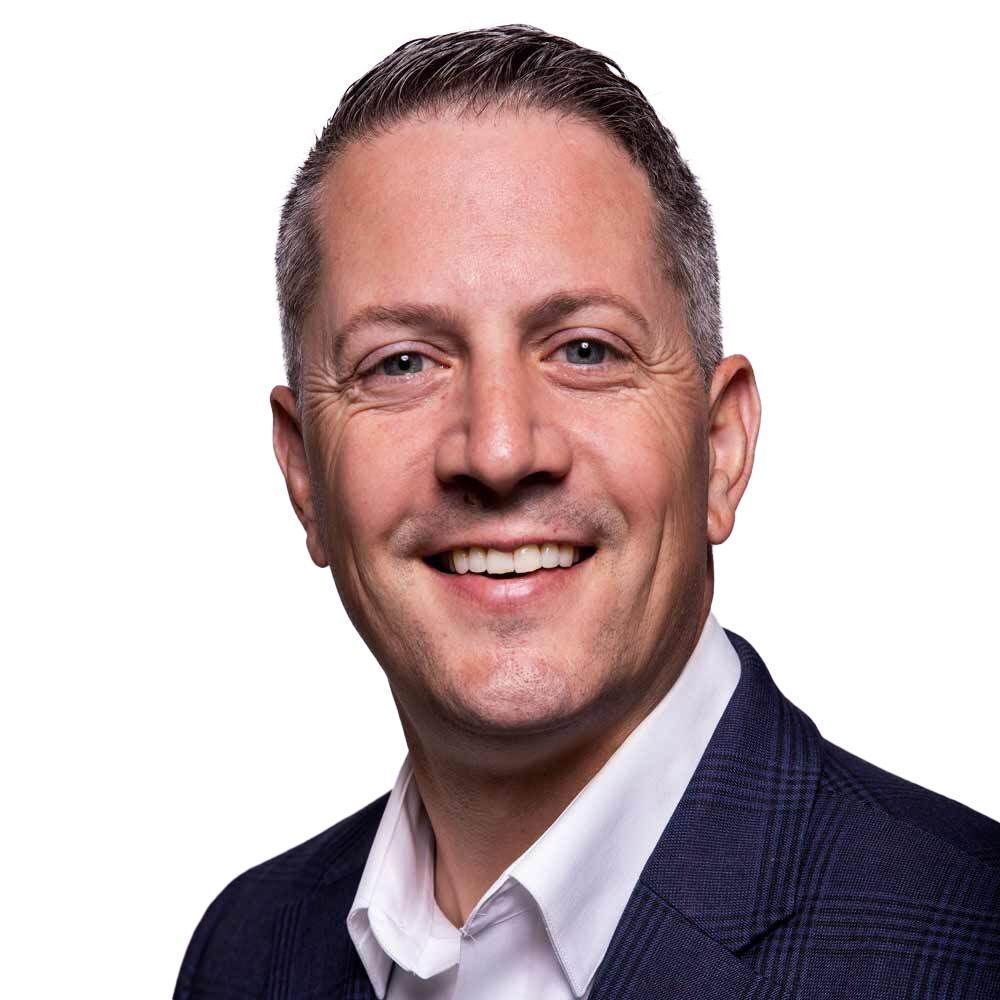
David Tibbetts, CSP
Highwire, Chief Safety Officer
David Tibbetts is a Certified Safety Professional and Chief Safety Officer at Highwire. His focus is on continued product development, client success, and customer support with the goal of helping Highwire clients deliver Contractor Success through full-lifecycle risk mitigation.